Wm. Hill & Son and Norman & Beard Ltd’ (also known as Hill, Norman and Beard) was formed in 1916 from the amalgamation of the two large organ-building firms – Hill & Son of London and Norman & Beard of Norwich.
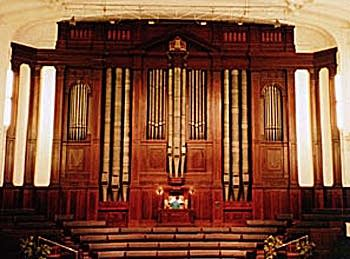
The business traded on its heritage looking after many of the large cathedral organs and also constantly updating its approach to organ-building so that it also played a large part in the Theatre and Cinema organ business of the 1920s and 1930s. The company was acquired by John Christie in 1924* and continued to open and close branch offices intermittently – there was also a branch of the business founded in Australia. Hill, Norman & Beard continued in existence until 1998*.
The Norman family
Although the Norman family is indirectly related to the John Norman who was Mayor of Norwich in 1714, our story starts with William Norman (1830–1877) working in London as a cabinetmaker for the London organ-builder J. W. Walker. Becoming interested in organs, William built a chamber organ for his own use and then his eldest son, Ernest W. Norman (1851–1927), took up an apprenticeship with J. W. Walker. Ernest fell out with Walker’s and moved back to Norfolk with his father, now ill with tuberculosis. The company was initially based in Diss, and it is interesting to note that there is an 1870 W. Norman & Son organ in the Baptist Church there.
William Norman died in 1877 and Ernest moved to Norwich, already advertising as ‘Ernest W. Norman, Tunist to the Cathedral’. Ernest’s younger brother Herbert J. Norman (1861–1936) became interested in the work and studied for a while with T. C. Lewis in London. By 1883 the business had moved to a larger workshop and took the name ‘Norman Bros.’, building its first three-manual organ for the church of St. Michael at Coslany, Norwich, in 1885. This was followed by their first four-manual instrument, built for the chapel of Jesus College, Cambridge, in 1887.
By this time the firm had become ‘Norman Bros. and Beard’, following the arrival of G. A. Wales Beard in 1885. By all accounts Wales Beard was no craftsman, but was a talented publicist and salesman. By 1886 they were advertising as ‘By Special Appointment to the Prince of Wales’. Thenceforth the firm was run by a triumvirate. Ernest specialised in mechanism, Herbert specialised in the voicing of the organ pipes and became a great friend of Alfred Hollins, the famous blind concert organist and composer, with Wales Beard as principal salesman. In later years Beard ran a separate sales office in Berners Street, London, which he styled ‘Head Office’ and himself as ‘Managing Director’.
Expansion
The business expanded rapidly, becoming ‘Norman & Beard Ltd’ in 1896 and, outgrowing the workshop again, moved in 1898 to a purpose-built factory in St. Stephen’s Road, Norwich, reputed at the time to be the largest organ-factory in Europe. The three-storey pipe-making workshop still exists, now converted to luxury apartments. A second factory in Ferdinand Street, Camden Town, London, was opened in 1902, initially managed by T. C. Lewis and later by Llewellyn Simon who, after 1916, went on to manage the Liverpool-based organ-builders Rushworth & Dreaper. By 1908 the firm had a staff of 300 and were building around 70 new organs a year — at least one instrument per week!
Some of the instruments made at this time were the 1899 five-manual organ for Norwich Cathedral, the three-manual organ for Colchester Town Hall and the four-manual organs for Wellington and Auckland Town Halls, New Zealand, and Cape Town Town Hall, South Africa. What were the reasons for this success? Firstly, the entrepreneurial (if not always very scrupulous) salesmanship of Wales Beard, and secondly, the efficiency of the Norwich factory plus the advantage of Ernest Norman’s tubular exhaust-pneumatic key-action which was simpler, easier to make and quicker to install on site than the charge-pneumatic actions of their rivals. Herbert J. Norman exploited a voicing technique that yielded new tone qualities by enabling narrow-scale pipes to speak properly and bass pipes to speak more promptly than before.
Voicing Technique
This voicing technique came to the firm with some key members of staff inherited from the debris of the Robert Hope-Jones Electric Organ Company when it went bust in 1899 (the owner later fleeing to America, allegedly to escape his creditors). Hope-Jones had developed a low-voltage electric action for organs, allowing the console to be some considerable distance away from the pipes. Herbert Norman having visited the pioneer 1887 Hope-Jones organ in Birkenhead, Wales Beard became a director of the Hope-Jones company and Norman & Beard became major suppliers of organ parts to the firm. Norman & Beard later used his electric action when a console needed to be detached, most notably in the 63-stop, four-manual 1914 instrument in the Usher Hall, Edinburgh.
Although Wales Beard was a clever salesman, his principal weapon was price; the three Town Hall organs for the southern hemisphere, made in the less efficient London factory, are rumoured not to have been profitable. The London factory was closed in 1910 and the loss of much of the relatively young workforce to fight in the 1914–18 War led to a reduced turnover. One surmises that the Norwich factory probably had a large mortgage on it. The last organ to be built in Norwich was the 97-stop, four-manual for Johannesburg Town Hall in 1916. In that year the firm merged with the long-established firm of Hill & Son of London. Norman & Beard had the sales but not the staff, whereas the reverse was true of Hill’s, the Hill workforce being older and less affected by the war. The Norwich works closed and the combined firm operated from the Hill factory in London.
John Christie of Glyndebourne,
Wm Hill & Son and Norman & Beard Ltd, generally known as Hill Norman & Beard, had an early client in a wealthy amateur who, in 1920, commissioned a 45-stop four-manual instrument for his specially-built music room. The client, John Christie of Glyndebourne, liked the organ so much he bought the company. He put the company into the new market for organs to accompany silent films. The instruments were known as Christie Unit Organs. They were based on American Wurlitzer technology which, in turn, had been based on patents granted to Robert Hope-Jones. Thus one of the facets of the Norman & Beard company had come full circle!
by John Norman
Great-grandson of William Norman
*information supplied by John Norman, organ consultant, November 2018
Thank you very much for your note with its good news that the organ is being restored. I am happy to give you permission to reproduce my notes on the history of Norman & Beard. The 1934 instrument would have been designed by my father, Herbert Norman.
Good fortune with the project.
John Norman